The word “concrete” comes from a Latin word, concretus, meaning to grow together—and that’s exactly what it does when you combine its three ingredients, which are:
- A mixture of coarse and fine aggregates (sand, gravel, stones, larger bits of crushed rock, recycled glass, bits of old recycled concrete, and pretty much anything equivalent)—typically 60–75 percent.
- Cement (the everyday name for calcium silicates and aluminates)—typically 10–15 percent.
- Water—typically 15–20 percent.
Thrown together and mixed well, these simple ingredients make a composite, which is the name we give to a hybrid material that’s better in some important way than the materials from which it’s made.
In the case of concrete, the “important” thing is that it’s strong, hard, and durable. Thinking of concrete as a composite material, the cement hydrate is the background, binding material (technically called the “matrix”) to which the sand and gravel add extra strength (the “reinforcement”).
From that point, Concrete is a composite material composed of fine and coarse aggregate bonded together with a fluid cement that hardens over time.
Concrete is the second-most-used substance in the world after water and is the most widely used building material.
Almost every kind of construction involves concrete in some way, and it’s used to build everything from highways to bridges and skyscrapers to parking structures.
Concrete is resilient in that it does not rust, rot, or burn. The use of concrete as a building material is essential to buildings due to its durability, strength, and extreme longevity.
Table of Contents
- What is concrete?
- Importance of Concrete.
- Concrete Ingredients.
- Mix Design
- What are the basic properties of concrete?
- How is concrete made?
- 16 Common types of concrete
- 1. Normal-strength concrete
- 2. Plain concrete
- 3. Lightweight concrete
- 4. Ready mix concrete
- 5. Polymer concrete
- 6. Glass concrete
- 7. Reinforced concrete [RCC]
- 8. Pervious concrete
- 9. Prestressed concrete
- 10. Precast concrete
- 11. Air-entrained concrete
- 12. High-strength concrete
- 13. Vacuum concrete
- 14. Asphalt concrete
- 15. Rapid set concrete
- 16. Self-compacting concrete
- Advantages of Concrete
- Concrete construction process
- Obstacles in the Concrete Construction Process
- Common Applications of Concrete Construction
- Choose The Right Concrete Grade For Your Project
- Top Concrete Facts
- Why is concrete such a popular building material?
- Frequently Asked Questions
- Popular On-Website for Engineers Right Now!
What is concrete?
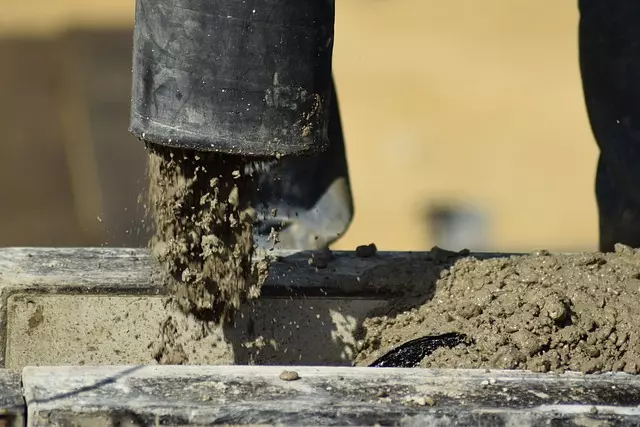
Concrete is a hardened mixture of paste and rocks, also known as aggregates, that is used as a building material for durable structures like buildings and bridges. When fresh concrete is initially mixed, it is pliable and plastic-like.
Hardened concrete, on the other hand, is sturdy and extremely tough.
Also Read: Structural Design Basis | General Guidelines
Importance of Concrete.
We are living in a concrete age. It has become so important because it is used in almost every type of construction: buildings, roads and highways, tunnels, storage dams and power generating plants, airports, and atomic power reactors.
Thus, in buildings, it is used almost from the foundation to the topmost story. In transportation, it is used in streets, highways, Airports, etc.
Concrete is also a material used extensively for water storage and transport, such as in the lining of canals and water reservoirs.
In addition to the above primary uses, it is also used as a coating material for specific purposes such as waterproofing, fireproofing, soundproofing, and shielding against radiation in X-ray plants and atomic power plants.
The essential property of concrete is that it sets and hardens into a strong, rock-like mass within a short period.
The ultimate strength and other properties of concrete depend on several factors, such as:
- The nature of the aggregate materials used.
- The quality and proportions of cement and aggregates.
- Water is used for making the mixture.
- And on the Workmanship.
The Composition is generally expressed in terms of relative volumes of:
- Cement.
- Fine aggregate (sand).
- And coarse aggregate (gravel, etc.)
Thus, a 1:2:4 concrete indicates a mix having 1 part by volume of cement, 2 parts of sand, and 4 parts of gravel or crushed aggregates.
In actual mixing, the relative volumes are converted to the weights of respective materials.
Also Read: Water Supply Design | Water Sources and Storage Tanks
Concrete Ingredients.
The following are the ingredients of concrete.
1. Binding material (Cement or Lime).
2. Fine aggregate (Sand or such other materials).
3. Coarse aggregate (Gravel, crushed stone, or such other materials).
And Water.
4. Admixtures are classed as optional ingredients.
The function of Binding Material.
The function of a Binding material (Cement or Lime) is to bind the coarse and fine aggregate particles together.
Although “Portland Cement” is the most common binding material used as a binder in a mixture.
Much research has been done to prove that lime (especially Hydraulic Lime) can also be used successfully as a Binding material in common types of construction.
Lime is economical as compared to cement and also strong enough for the ordinary type of construction.
The function of Aggregates.
The function of Fine aggregates serves the purpose of filling all the open spaces in between the coarse particles. This way, the porosity of the final mass is decreased.
The maximum particle size in fine aggregates is always less than 6.35 mm. However, sand is commonly and universally used as a fine aggregate, and its grain size is around 2 mm.
The function of Coarse aggregates is to act as the main load-bearing component of concrete.
When a good number of coarse aggregate fragments (all more than 6.35 mm in diameter) are held together by a cementing material, their behavior towards the imposed loads is just like a very strong rock mass.
Gravel and crushed stone are commonly used for this purpose.
The function of Water.
Water is the main component of the concrete mix. Water plays an important role in the process of the chemical reaction of cement and aggregates.
The function of Admixtures.
Admixture affects the setting time of cement, and they are used mostly for specific purposes.
Also Read: Landfill: General Overview You Should Know In 2023
Mix Design
Modern concrete mix designs can be complex. The choice of a concrete mix depends on the need of the project both in terms of strength and appearance and in relation to local legislation and building codes.
The design begins by determining the requirements of the concrete. These requirements take into consideration the weather conditions that the concrete will be exposed to in service and the required design strength.
The compressive strength of concrete is determined by taking standard molded, standard-cured cylinder samples.
Many factors need to be taken into account, from the cost of the various additives and aggregates to the trade-offs between the “slump” for easy mixing and placement and ultimate performance.
A mix is then designed using cement (Portland or other cementitious material), coarse and fine aggregates, water, and chemical admixtures. The method of mixing will also be specified, as well as the conditions which it may be used.
This allows a user of the concrete to be confident that the structure will perform properly.
Various types of concrete have been developed for specialist applications and have become known by these names.
Concrete mixes can also be designed using software programs. Such software provides the user an opportunity to select their preferred method of mix design and enter the material data to arrive at proper mix designs.
What are the basic properties of concrete?
The basic properties of concrete are fine and coarse aggregates (like sand and rocks or pebbles), Portland cement, and water.
These three raw materials each play a different chemical role in the formation of concrete, as Portland cement is a hydraulic cement, meaning it gets its strength from its chemical reaction with water.
When Portland cement and water combine, a chemical reaction called hydration occurs. Through this process, the paste coats the aggregates and bonds them together, gaining strength as it hardens, and concrete is created.
When making concrete, builders use fine aggregate to add volume, while coarse aggregate provides the strength necessary to carry heavy loads.
Various chemicals, called admixtures, can also be added to concrete to make different sorts of mixtures.
How is concrete made?
Before concrete is made, the three raw materials must be proportioned correctly to ensure the outcome of a mixture that is strong and sturdy.
The components of concrete react differently with each other based on the ratio of how much of each is added, and proportions will differ based on the type of concrete being made. The most common ratio, however, is:
- 10–15% cement
- 60–75% aggregate
- 15–20% water
The concrete mixing process begins with preparing the Portland cement mix. Portland cement is made of a calcareous material (often limestone) that is ground up into a powder, which is then heated and burned in a rotary, turning it into a pebble-like material called “clinker” The clinker is then ground up again until it is a crushed powder, to which gypsum is added.
After the Portland cement is prepared, it is mixed with the aggregates, water, and optional admixtures (the different chemicals or materials that change the consistency and strength of concrete).
The ingredients are stirred together well to properly coat the aggregates with the cement paste.
After combining the materials, the cement is activated by the water, coating the aggregate particles and gaining strength as it hardens in a process called hydration.
Also Read: Biggest Cement Companies in the USA in 2022
16 Common types of concrete
One of the reasons concrete is used to build so many different structures is due to how versatile it is and how it can be molded to any desired shape or design. There are many different types of concrete, however, and they are used for all different sorts of structures. Here are 16 types of concrete and how they are used.
1. Normal-strength concrete
Normal strength concrete, or “regular” concrete, is the most common type of concrete with a basic mix of cement, aggregates, and water.
Normal concrete has a mixing proportion of 1:2:4 (one part cement, two parts aggregate, and four parts water), however, the amount of water used will depend on the humidity of the location and the desired consistency of the concrete.
Normal-strength concrete is typically used for pavements, home construction projects, and buildings that don’t require maximum tensile strength.
2. Plain concrete
Plain concrete is concrete in its simplest form. It is made using the same mixing proportions as normal strength concrete but will have absolutely no reinforcement in it.
It can be used to build structures that do not require intense tensile strength. Pavements and walkways are common uses of plain concrete.
3. Lightweight concrete
This type of concrete has a lower density and a higher water content than normal concrete. Lightweight concrete is made using lightweight aggregates, such as pumice, clay, or perlite.
Since the specific aggregates chosen are what determine the density of the concrete, lightweight concrete is low in density and is defined as any type of concrete with a density level of less than 1920kg/m3.
Lightweight concrete is used in areas where the total “dead weight” of a building can be reduced to help prevent collapses, such as walls or flooring.
4. Ready mix concrete
Ready-mix concrete is made at a manufacturing plant and delivered to a construction site using a truck with a mixer attached to it. It usually contains admixtures to make it so the cement doesn’t harden before arriving at the site and is ready to pour.
5. Polymer concrete
Polymer concrete is concrete in which the lime and shale-based Portland cement is replaced with a polymer binder that cures and hardens, such as a polyester, epoxy mixture, vinyl ester, acrylics, or many various types of polymer resins. The objective of polymer concrete depends on the type of resin used.
Epoxy binders, for example, will aid in less shrinkage during curing, while acrylic binders offer weather resistance and quicker setting times.
Polymer plastic is stickier than cement, and therefore, when combined in a concrete mix, leads to the concrete of higher tensile strength than one composed of Portland cement.
When mixing together a polymer binder with water and aggregates, a chemical reaction occurs that begins the curing process quicker than regular concrete.
Polymer concrete has a good resistance to corrosion, which is why it is used in swimming pools, sewer structures, and other structures that come into close contact with liquids and corrosion-causing chemicals.
6. Glass concrete
Concrete is referred to as glass concrete when recycled glass is added as an aggregate or used in places of both fine and coarse aggregates, depending on the desired outcome.
Glass aggregates are almost always made from recycled glass and can range in size from fine talc-like powder to gravel-sized pieces to six-inch glass rocks.
A Glass can be crushed using a glass-crushing machine or used in chunks when mixed with the cement, depending on the desired look.
Glass concrete typically has a shiny or “glowing” look to it, which makes it an aesthetically pleasing and highly polished-looking option for countertops, floors, and tiles.
7. Reinforced concrete [RCC]
Reinforced concrete, also known as reinforced cement concrete, is made with reinforced bars, usually rebar, to improve the tensile strength of the concrete.
The compressive strength of the concrete, paired with the tensile strength of the reinforcement material, improves the concrete’s overall durability.
Contractors might encounter reinforced concrete in large-scale structures that require an immense amount of tensile strength, such as tall buildings, bridges, dams, or any construction situation that involves a structure needing to carry extremely heavy loads.
Also Read: 15 Types of Windows Every Homeowner Should Know In 2023
8. Pervious concrete
Pervious concrete is a more porous type of concrete that lets water pass through it to groundwater underneath.
This type of concrete is used to build roads and pavements and is designed to deal with stormwater buildup and can absorb water at a rate of up to five gallons a minute.
There are little to no fine aggregates in this type of concrete, creating more voids for water and air to pass through.
This allows stormwater to be filtered through the concrete and pass through into the ground. Pervious concrete can help prevent flooding since the water that would normally flow through storm drains is absorbed by the earth.
9. Prestressed concrete
Prestressed concrete is concrete that has compressive stresses applied to it during production and combines the high tensile strength of steel and the high compressive characteristic of concrete.
These initial compressive stresses are induced by steel tendons located inside of or adjoining to the concrete and are engineered to counteract the stresses that will eventually be placed upon the concrete during service.
Since it has been formed under stress, a prestressed concrete structure will be more balanced and less likely to crack when carrying heavy loads. Bridges, roofs, water tanks, and floor beams are often made using prestressed concrete.
10. Precast concrete
Precast concrete is concrete that is poured in a mold and cured, usually offsite, and then transferred to a construction site.
This allows for the concrete to be created in a more controlled environment, like a plant or a factory, with more oversight and surveillance, which is good for quality control.
Factories can also use the same molds over and over again, saving time and money. Precast concrete allows for speedier construction, as it shows up to the construction site ready to be installed without any waiting time for it to gain strength.
Precast concrete also improves time efficiency in that the walls of a structure can be made off-site as the foundation is created on-site, resulting in the building being ready for use faster.
11. Air-entrained concrete
Air-entrained concrete is concrete containing microscopic air bubbles that help to relieve internal pressure in the concrete.
An air-entraining agent is added during the mixing process, reducing the surface tension and causing air pockets to form in the slurry.
This type of concrete is suitable for structures in environments with freeze-thaw conditions, where the temperature shifts from below to above freezing, causing a water buildup.
The tiny pockets allow space for water to expand, which prevents cracking and resists scaling in concrete, resulting in a structure that lasts longer over time.
The microscopic air bubbles range from 5–7% of the concrete mix, and since adding air to concrete lessens its density, it is common for a higher amount of cement to be used to make up for the strength.
12. High-strength concrete
High-strength concrete is any concrete that has a compressive strength of 6000 pounds per square inch (PSI) or higher.
It is made using strong, durable aggregates and has a high cement content and lower water-to-cement ratio, with superplasticizers added to improve any workability issues stemming from stickier concrete.
Compared to normal-strength concrete, the primary use of high-strength concrete is to reduce the weight, bleeding, and permeability issues, making the structure more resistant to corrosion and chemicals.
High-strength concrete is commonly used in the construction of high-rise buildings servicing highly compressive loads.
13. Vacuum concrete
Vacuum concrete is concrete involving the removal of excess water not needed for the hydration process after the concrete is placed and before the hardening process begins.
Mats are placed on filtering pads over the cement, and a vacuum pump is used to extract the excess water.
This technique, called vacuum dewatering, lowers the water-to-cement ratio of the concrete, which gives vacuum concrete a higher strength and durability level compared to normal concrete.
It also has a high workability level, despite high strength and workability not usually being achievable simultaneously in concrete.
This is due to the excess water, making it easier to pour. After pouring, the water is no longer necessary and is vacuumed out to achieve high strength. Bridge deck slabs and industrial floors are common uses of vacuum concrete.
14. Asphalt concrete
Asphalt concrete is a type of concrete commonly used to make roads, parking lots, and other pavement types.
It’s a composite material composed of two primary ingredients: aggregates and liquid asphalt, which are typically combined at a plant and transported to a paving site and spread by a paving machine, followed by being compacted by rollers. The result is smooth pavement.
15. Rapid set concrete
Rapid set concrete is a type of concrete that hardens at a quicker pace than normal concrete, usually within one to several hours compared to the usual 48 hours.
This is because the cement content of rapid-set concrete is higher than regular concrete, and it also has admixtures added to the mix that work to quicken hydration and the hardening process.
Rapid-set concrete comes premixed and is ready to use, which is why it is commonly used for non-structural concrete jobs, such as concrete repair and restoration.
16. Self-compacting concrete
Self-compacting concrete, or self-consolidating concrete, is a type of concrete with three key properties: a high filling ability, enabling it to flow with ease throughout the formwork when poured, as dispersed by its weight; a high passing ability enabling it to pass around any confined spaces and obstructions like steel reinforcement; and segregation resistance, or remaining the same state, during transport, placing, and after placing.
These qualities make it so that the concrete sets into the mold very closely without requiring any further assistance or vibration, making it a good option for construction jobs involving less labor and a faster placement time.
The fluidity in this type of concrete is due to it being made with a higher count of fine aggregate, usually sand, combined with the use of additives like viscosity-enhancing admixtures and superplasticizers, which ensures that the sand particles are dispersed uniformly.
These additives, in addition to the usual ingredients of cement, fine and coarse aggregate, and water, are combined in a concrete mixer to form this type of concrete.
Also Read: Walls: Load Bearing Wall and Non-Load Bearing Wall
Advantages of Concrete
1. Durability
Most concrete buildings are designed to last at least 30 years in service, although many last long before deteriorating to the point of repair or replacement.
Concrete is so durable and long-lasting that buildings made from it are rarely demolished due to deterioration.
Instead, they become obsolete and suitable for repurposing or demolition for new construction.
Concrete is highly resistant to damage and abrasion from high humidity and rain. It has hardly any organic content that can rust or rot, so moisture can only attack joints. Annual joint maintenance ensures that a concrete building remains impermeable to moisture.
Concrete is the best material for house construction in areas susceptible to extreme weather.
One particular home provides a shining example of concrete’s durability. The Sundbergs were a family determined to build their home on the hurricane-prone coast of Mississippi. After studying a variety of Federal Emergency Management Agency (FEMA) maps and building codes, they decided to build with concrete.
They designed their home with Insulated Concrete Form (ICF) walls and used concrete for beams, columns, roofs, and floors in the home.
At only 85 percent of the completion of the house, Hurricane Katrina tore through the area. Aside from a good number of shattered windows, the home was completely intact.
Concrete construction allowed the house to withstand 180 to 220 mph winds and 28-foot flood waters.
2. Fire Resistance
Water and wind aren’t the only elements concrete defies. Concrete is fireproof, and even if the interior of the home suffers fire damage, the concrete shell will escape unscathed. Home structure fires are an inherent hazard with most building materials.
Each year, United States fire departments respond to more than 355,000 house fires that cause an average of $6.5 billion in property damage.
While fire is a risk in any geographic location, those who live in areas with notable wildfire risks should give even more consideration to concrete when building a home.
The devastating Carr wildfire in Northern California destroyed 1564 homes and claimed several lives in the process.
In the aftermath, many residents are considering how to fireproof new homes — and concrete makes an attractive option.
3. Cost
The up-front cost to build a new concrete home is higher than that of wood or steel frame homes. The difference in cost tends to fluctuate as the price of steel moves up and down, while the price of concrete stays relatively stable.
At the national average, a concrete house will cost between 4 and 8 percent more than a steel or wood frame home.
When you’re already talking about hundreds of thousands of dollars, that small percentage can add up to a significant price tag.
However, concrete homeowners enjoy a substantial reduction in energy costs over time. According to the U.S.
Department of Housing and Urban Development (HUD), concrete construction saves homeowners 20 and 25 percent monthly on their energy costs.
In other words, the upgrade to concrete pays for itself.
Insurance costs for concrete homes are notably lower, as well, since the houses are significantly less susceptible to damage of all varieties.
Also Read: Best Laptops for Engineering Students: The Complete Guide 2023
4. Construction cost
The speed of construction for a concrete building depends on the type of concrete, but it’s generally comparable to wood frame construction and markedly faster than structural steel.
Because steel must be fabricated off-site and transported, the process takes longer than pouring and erecting a concrete slab.
When using a cast-in-place concrete plan, builders can implement a two-day cycle. This intensive cycle allows workers to complete up to 20,000 square feet of floor in 48 hours.
5. Energy efficiency
Concrete is a good insulator, making it a great choice for regulating temperatures in both hot and cold environments.
Since it has fewer spaces for air to move through, less energy is needed to keep a building warm or cool.
This low permeability means that concrete can help maintain temperatures even during long periods without heat or power, so it’s often used for shelters.
With these qualities, many homeowners and business owners can reduce their energy bills by building with concrete.
Using ICFs can offer additional insulation for better performance. Producing concrete is also more energy-efficient than making other types of building materials, like steel and aluminum.
6. Versatility
Concrete is highly malleable when mixed and can take on various additives, appearances, surface textures, and shapes. We see new types of concrete being made every year, including blends with high-performing characteristics to suit specific applications.
Concrete can be used in specialty projects and adapted to fit even the most unique projects. Plus, it doesn’t need special conditions to set, so it can harden at ambient temperatures.
Characteristics like moisture and high-temperature resistance make concrete a good fit for settings with these demands, like underwater construction and high-heat factories.
7. Low maintenance
The maintenance costs of properly installed concrete are little to none, with many applications lasting for decades. While you might choose to coat or repaint concrete for aesthetic reasons, doing so isn’t required to maintain its structural performance.
Building owners may find that concrete construction lowers maintenance demands due to reduced risks of poor air quality, moisture damage, fading or wear from sunlight, pests, and structural problems. As a result, homeowners and building managers may need to spend less on replacing components, setting up costly ventilation systems, or spraying for vermin.
Also Read: Process of Manufacture of Cement
Concrete construction process
The construction of concrete buildings differs in many ways from the traditional process, and there are multiple ways to go about it.
The two most common types of concrete structures for residential and office buildings are tilt-up and ICF.
Before beginning, both construction methods require workers to excavate the site and prep the subgrade. Once the site is ready, the two methods diverge.
1. TILT-UP CONSTRUCTION PROCESS
Tilt-up construction is almost self-explanatory. Once large slabs of concrete are dry, machinery tilts them up and into place. The process goes as follows:
- Workers first create footings for the slab panels. These wood bars define the size and shape of the panels. All doorways and windows are included in the initial form, so there’s no room for error in following the design.
- The workers incorporate the rebar lattices into the forms. They also create inserts where the crane will hold and lift the slab, as well as embeds where the panels will attach to floors, the roof, and other panels.
- Once the forms are completely clean and dry, workers pour the concrete in and wait for the panels to dry.
- Workers remove the forms and attach cables to the crane.
- The crane lifts and tilts the slab until it hovers vertically above the ground, at which point workers push the slab into the right position.
- The crane carefully lowers the slab down. Workers brace the panel and connect it to the footing.
Once the crane disconnects from the finished panel, the crew is ready to rinse and repeat as many times as they can for the day.
2. ICF Construction process
Insulated concrete forms come in a few different types, but they all function on the same design principle.
Each block consists of two insulating faces, usually made of polystyrene. The two faces are connected by metal connectors, plastic, or more polystyrene with space in the middle. The construction process is simple but requires precision:
- After preparing the site, workers create a footer that will work with a particular ICF system.
- Workers stack the ICF units in layers. Many ICF blocks have interlocking grooves at the top and bottom to make stacking blocks fast and easy.
- Workers brace walls heavily to ensure they remain straight and install rebar in the blocks according to manufacturer specifications.
- Workers re-check the bracing, and once they confirm the wall is still straight, it’s time to pour the concrete. A concrete pouring truck is traditional, but builders can simplify and speed up the process with the use of a concrete boom pump.
- Once the concrete dries and cures — usually within three to five days — the bracing comes off. The building is now ready for wiring through the foam surface, as well as for interior and exterior finishing.
Also Read: What is Bitumen? | Types and Tests of Bitumen
Obstacles in the Concrete Construction Process
Building with concrete (especially ICF) is no more complicated than building with traditional materials. However, some unique issues can plague novice concrete builders. Here are a few tips to help things go smoothly for a beginner:
- Use Enough Fasteners: Attaching the recommended number of fasteners during ICF construction is time-consuming, and some builders will cut corners by ignoring the recommendations. This practice is dangerous and degrades the durability of the completed building.
- Triple-Check Your Plans: The main disadvantage of concrete vs. other materials is the lack of flexibility for last-minute changes. If you find a flaw or mistake in your building plan, you won’t be able to alter it after the concrete starts flowing. Putting a window in the wrong place may not be a deal-breaker, but it’s critical to be more safe than sorry with concrete.
- Don’t Risk Blowouts: Experienced builders know how much pouring ICF blocks can handle at a time. Pushing that limit risks a “blowout,” where rapidly poured concrete breaks through the polystyrene blocks. When this happens, the cost of wasted concrete and the effort of cleanup may cause profound delays.
As with any construction project, having an experienced professional in the loop makes costly mistakes less likely.
Also Read: Best Engineering Universities in the USA
Common Applications of Concrete Construction
Now that the convenience and cost benefits of concrete house construction are clear, it’s worth exploring three of the more specific reasons people and companies choose concrete.
1. To stay up to code
Most states and jurisdictions in the United States adopt some form of the codes set forth by the International Code Council (ICC). The ICC evaluates and updates building codes every three years, but there is no obligation for states and communities to actually follow those codes.
In 2016, Louisiana experienced catastrophic flooding after prolonged rainfall — 31 inches of rain in 15 hours led to mass power outages and flood damage to at least 40,000 homes.
Yet, despite the overwhelming destruction, Louisiana decided it wasn’t necessary to add to the building code the ICC mandate requiring the bottoms of buildings to rise one foot above base flood elevations.
Many builders of homes or other constructions have good reason to want their buildings to exceed the minimum codes in their community.
Reinforced concrete passes muster with any building code and often far exceeds the minimum requirements for ICC compliance. In areas prone to extreme weather events or temperatures, concrete is undoubtedly the best material for house construction.
2. To cut down on noise
Concrete affords comfort in addition to safety. Noisy neighbors and loud music from the other room cause far less discord than they would in a traditionally framed home because concrete is excellent at sound dampening.
In comparison to a wood-frame wall, only an eighth to a quarter as much sound will penetrate a wall made from ICF blocks. This property makes concrete an ideal solution for settings that benefit from noise blocking. Think office buildings, schools, or apartments.
Also Read: 12 Most Expensive Colleges /Universities In The World
3. To improve healthcare settings
Concrete even has health benefits over other materials, making it highly suitable for environments like hospitals and private practices. Concrete buildings have minimal levels of air infiltration.
When air can’t get into a building, it’s easier to control and filter the air circulating indoors. Lack of air infiltration also significantly reduces unwanted moisture.
As a structural element, concrete offers better vibration control and sound dampening to benefit both patients and staff in a medical facility.
Studies on noise levels in hospitals show that too much commotion affects how well patients recover and how well staff members can focus on their jobs.
Reducing building vibration can improve the function of increasingly fine-tuned machines, as well as decrease strain on surgeons performing delicate procedures.
Certain forms of concrete featuring calcium aggregates also block more radiation than any other construction material. Facilities that perform radiation therapies are particularly suited to concrete builds.
Choose The Right Concrete Grade For Your Project
Whether you are working on patio slabs, pathways, pavement curbs, floor binding, domestic floors, foundations, roadways or commercial structures, you need the right concrete grade to extend their durability.
In other words, if you are working on a residential project or a commercial project, for that matter, investing in the right concrete grade remains the primary step toward building robust structures.
The strength of the concrete and its composition are two crucial factors that distinguish one grade from another.
To produce the type of concrete you want, you need to maintain a precise ratio of cement, water, and aggregate, which is made up of sand and stone; otherwise, you won’t be able to get the right strength and composition.
So, if you are planning to order quality concrete for your project, you must be aware of the different grades of concrete and their uses.
C5/7.5 Concrete
Used in both commercial and domestic projects, C5 or C7.5 is a wet lean mix concrete. It is an ideal option for foundations and blinding when you are working on a residential project. Besides, it is also common among builders when it comes to working on curb bending.
C10 Concrete
Used for constructing patio slabs and pathways; C10 concrete is ideal for both domestic and commercial projects. It is also the perfect option for blinding house floors, trench fill, and foundation for steps.
C15 Concrete
C15 concrete is the right choice for constructing foundations for small walls and paving for steps. Besides, you can also use it for building sheds & conservatories. Construction professionals also prefer it for house floors.
However, if you use any other grade of concrete for constructing these parts, you won’t be able to get the kind of finish you need.
C20 Concrete
It is suitable for domestic applications such as garages, sheds, driveways, paving for patios, and foundations for walls. It is also an ideal option for internal floor slabs.
C25 Concrete
Suitable for a variety of applications like footings and foundations, trench fill, and reinforced fill, C25 concrete is a highly multifunctional concrete, and its demand is increasing day by day.
C30 Concrete
Used for constructing roadways, pathways, driveways, and garages, C30 concrete is an ideal option for enhancing the durability of the concrete structure.
C35 Concrete
It is an appropriate option for constructing durable commercial structures. You can use it for building foundations and beams, which are crucial for providing structural support to buildings and structures.
C40 Concrete
C40 concrete is the most durable concrete, and it is suitable for commercial construction.
Apart from that, you can also classify concrete as regular concrete, lightweight concrete, sand-mixed concrete, fiber-reinforced concrete, and gravel-mixed fiber-reinforced concrete.
In layman’s terms, regular concrete is nothing but a type of concrete that is ideal for pathways, patios, and other similar projects.
Similarly, lightweight concrete is also the perfect option for similar projects. However, you can use it in light spread to cover a larger area. You can maintain the same ratio of cement and aggregates.
If you talk about sand-mixed concrete, it is way too light when compared to other forms of concrete. Fiber-reinforced concrete offers extra safety because of the support of wires and metals.
In case you are looking forward to using a substitute for sand-mix concrete, gravel-mixed, fiber-reinforced concrete is the perfect option. It is thicker than sand mix concrete and helps in enhancing the durability of the structures.
Top Concrete Facts
- In ancient times, the Romans used it for building
As you may already know, concrete is extremely durable if mixed correctly with other materials. It will also need to be cured correctly if it is to last the test of time. But how do we know that concrete was used in ancient Rome? Well, structures built using this material are still in existence today.
A classic example is the Pantheon. The dome of this structure is made of concrete that is unreinforced and is the largest in the world.
The cement was made by mixing pozzolana, a type of volcanic ash, with slaked lime. After the Roman Empire had fallen, the knowledge of making cement had been forgotten by the Romans.
However, during the 18th century, the skill was revived. The other popularly known structures that were made out of concrete include the Panama Canal, the Hoover Dam, and the Three Gorges Dam.
- It becomes stronger when it stays wet for long durations
Concrete is made by mixing cement, water, and other materials. During the process of making concrete, a chemical reaction between the cement and water takes place. This is what strengthens the concrete, after all.
So, if you want your concrete to be stronger, ensure you keep it wet for as long as possible. Builders know this, and this is why they don’t let it dry out too quickly (hence all the barriers around wet cement). On average, it should be kept wet for at least three days.
- Over the years, concrete gets stronger
When properly mixed, poured, and cured, it gets stronger as time goes by. It will continue to strengthen for decades.
The explanation for this is based on the fact that calcium hydroxide that is found in cement turns into calcium carbonate when it absorbs carbon dioxide. The product, calcium carbonate, is not soluble in water and commonly exists in rocks such as limestone and marble.
The rate at which concrete becomes hardened is negatively affected by extremely cold temperatures.
Therefore, if cement is to be poured during the cold winter months, it must be protected. When crystals of ice form in the cement, proper hardening is hindered. This eventually leads to weaker concrete.
This is why it needs to be protected from the atmospheric air so that freezing can be prevented by the heat resulting from making the cement.
- Concrete can be modified to appear like other more expensive materials
With the rise of many new technologies, concrete can imitate more costly materials.
Examples of such materials include porcelain, cobbles, wood, ceramic tiles, travertine or granite, leather, or brick.
Hence, it can be used for countertops and floors in office buildings or residences. When polished well, it can have a matte finish or glisten. You are also able to stain, dye, or stamp concrete, which gives it many possibilities.
Why is concrete such a popular building material?
In cities, at least, concrete is everywhere you look—and it’s not hard to understand why. It’s easy to make from cheap and readily available ingredients, easy to pour into molds and make into all kinds of shapes (because it starts life a very viscous liquid), and it’s both fireproof and (relatively) waterproof.
But the main reason it’s so widely used in buildings is that it’s extremely strong in compression: you can squeeze it or stand a great deal of weight on it. It’s widely used in walls and foundations (the vertical supports, in other words) because it’s great for resisting weight piled on top.
Unfortunately, concrete’s very big drawback is that it’s about 10 times weaker in tension than in compression. It cracks or snaps easily if you bend or stretch it unless you reinforce it with steel inside, so it’s not much use in horizontal beams.
Although concrete looks heavy and monolithic, it’s much lighter than you might suppose: it’s about a fifth as dense as lead, a third as dense as steel, 10 percent less dense than aluminum, and only fractionally denser than glass.
Although concrete is often mixed on-site and formed into whatever shapes are needed at the time, it can also be supplied in precast “modules”; blocks, beams, wall sections, pavements, and cladding can all be made this way.
Giant, modern segmental bridges, for example, are often quickly and inexpensively assembled from identical concrete sections that have been precast in a factory and shipped to their final location.
That makes them quicker and easier to construct than if the entire bridge had to be cast in situ, which is much harder to do in the middle of a river, for example, or in adverse weather conditions.
Another option is to make concrete structures that combine some precast sections with other sections formed on-site.
Frequently Asked Questions
Why is concrete so commonly used?
Concrete is one of the most used construction materials. The mixture of cement, aggregates, and water gives it high compressive strength, impermeability, consistency, and resistance to aggressive environments and conditions like fires, and it is easy to handle, so all these characteristics make it one of the best materials.
What are the uses of concrete in buildings?
Concrete is used in buildings in structures, foundations, walls, floors, and also some decorative elements.
Other elements of construction where it is used are in the pavement of roads, bridges, dams, and pipes.
We hope this article helped you learn about the 16 Different Types of Concrete You Should Know Right Now. You may also want to learn about Concrete |Definition, Ingredients, and Curing You Should Know, What is Mortar? | Uses and Tests, Aluminium and Copper as Building Materials, and Brick Masonry | Advantages and Disadvantages In 2023.
If you liked this article, please join WebsiteForEngineers on Telegram, and you can also find us on Pinterest, Twitter, and Facebook.